Temperature sensors are critical devices that measure the thermal energy of an object or environment, converting it into a readable signal for monitoring and control purposes. These sensors are indispensable across industries, from manufacturing to healthcare, enabling precise temperature regulation, safety, and efficiency. This article provides a detailed exploration of temperature sensors, covering their definition, types, and applications in the process industry, automotive sector, medical field, and daily life. Key types such as thermocouples, Resistance Temperature Detectors (RTDs), thermistors, and others are discussed, with a focus on their widespread use and specific applications.
1. What is a Temperature Sensor?
A temperature sensor is a device that dettects and measures the temperature of a medium (solid, liquid, or gas) and converts this measurement into an electrical or digital signal. These signals are used by control systems, such as programmable logic controllers (PLCs) or microcontrollers, to monitor processes, trigger actions, or display data. Temperature sensors operate based on physical principles such as resistance change, voltage generation, or thermal expansion, depending on the sensor type.
Working Principle
Temperature sensors function by detecting changes in physical properties caused by temperature variations. For example, some sensors measure changes in electrical resistance, while others generate a voltage or use optical methods to infer temperature. The output is typically proportional to the temperature, allowing precise monitoring and control. Sensors are designed to operate in diverse environments, from extreme industrial conditions to sensitive medical applications.
Applications
Temperature sensors are ubiquitous across industries and daily life due to their versatility and precision. Key applications include:
- Industrial Processes: Monitoring and controlling temperatures in chemical reactors, furnaces, and pipelines to ensure product quality and safety.
- Automotive: Regulating engine performance, cooling systems, and cabin climate control.
- Medical: Measuring body temperature, monitoring incubators, and ensuring proper sterilization conditions.
- Consumer Electronics: Preventing overheating in smartphones, laptops, and appliances.
- Environmental Monitoring: Tracking weather conditions, greenhouse climates, and HVAC systems.
- Food and Beverage: Ensuring safe storage and cooking temperatures.
- Aerospace: Monitoring engine and cabin temperatures in aircraft.
Importance
Temperature sensors are critical for optimizing processes, enhancing safety, and reducing energy waste. In industrial settings, they prevent equipment damage due to overheating. In healthcare, they ensure accurate diagnostics and patient comfort. In daily life, they enable energy-efficient appliances and climate control systems.
2. Types of Temperature Sensors
Temperature sensors are broadly classified into contact and non-contact types based on their interaction with the measured medium. Contact sensors physically touch the object or medium, while non-contact sensors use radiation or optical methods. Below is a comprehensive list of temperature sensor types, including widely used and specialized variants.
Contact Temperature Sensors
- Thermocouples:
- Principle: Operate based on the Seebeck effect, where a voltage is generated at the junction of two dissimilar metals due to a temperature difference.
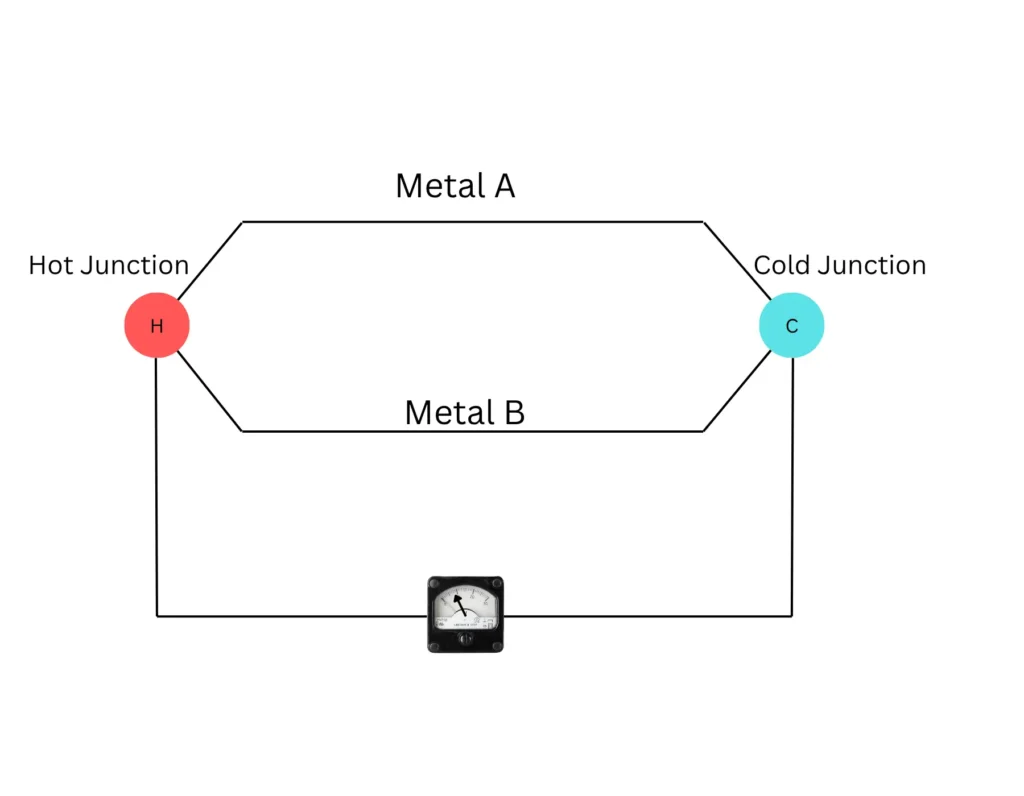
- Types: Common types include Type K (chromel-alumel), Type J (iron-constantan), Type T (copper-constantan), and Type E (chromel-constantan).
- Range: -200°C to 2000°C (varies by type).
- Advantages: Wide temperature range, rugged, and cost-effective.
- Disadvantages: Lower accuracy compared to RTDs, requires cold junction compensation.
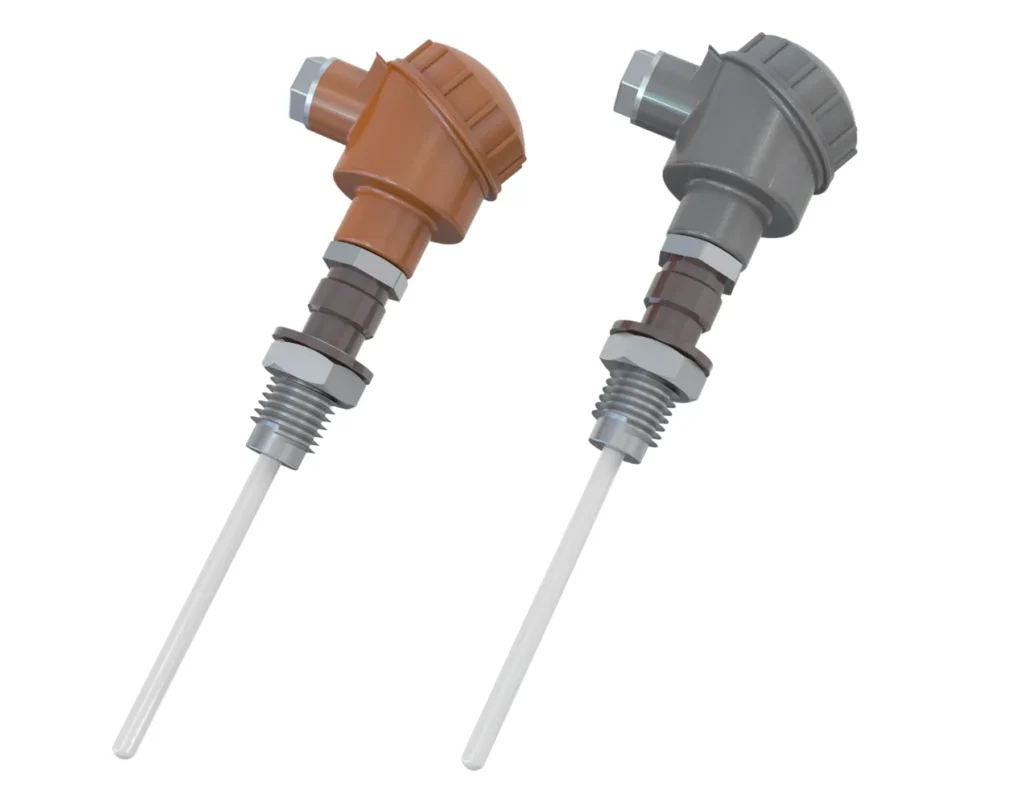
- Resistance Temperature Detectors (RTDs):
- Principle: Measure changes in electrical resistance of a metal (typically platinum) as temperature changes. Resistance increases linearly with temperature.
- Common Material: Platinum (Pt100, Pt1000).
- Range: -50°C to 500°C (extendable to 850°C with specialized designs).
- Advantages: High accuracy, stability, and linearity.
- Disadvantages: Higher cost, slower response time compared to thermocouples.
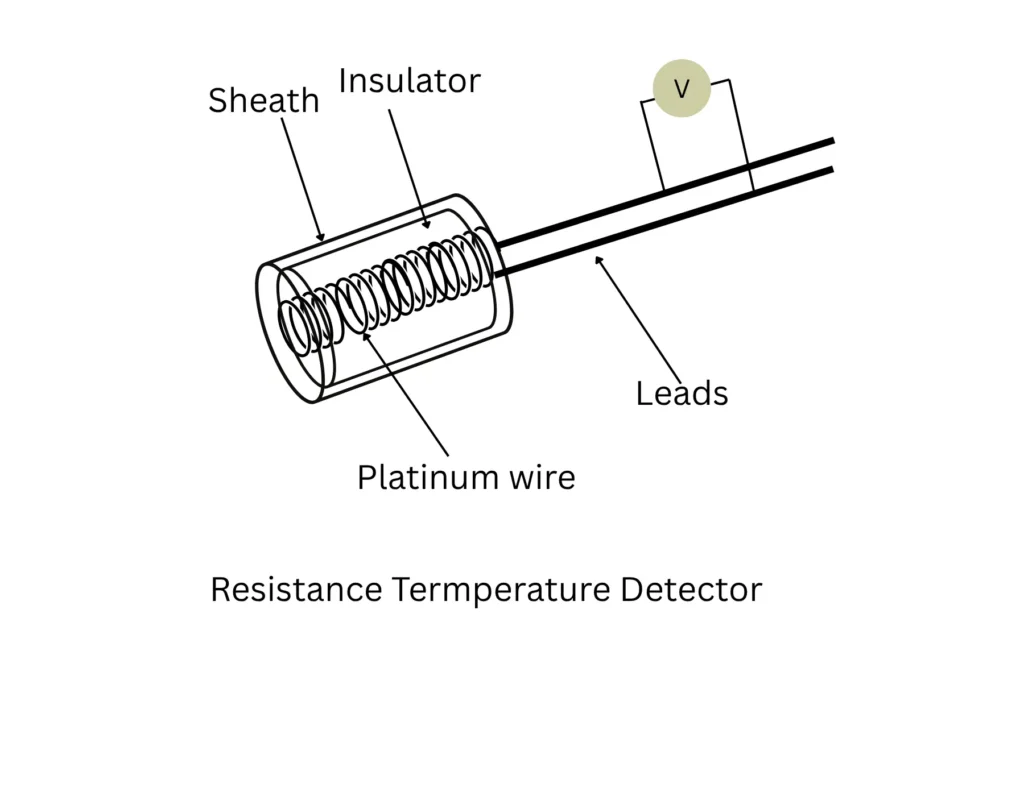
- Thermistors:
- Principle: Use temperature-dependent resistance changes in ceramic or polymer materials. Two types exist: NTC (Negative Temperature Coefficient) and PTC (Positive Temperature Coefficient).
- Range: -50°C to 150°C (extendable for specific applications).
- Advantages: High sensitivity, compact size, and cost-effective.
- Disadvantages: Non-linear response, limited temperature range.
- NTC Thermistors:
- Principle: Resistance decreases as temperature increases, offering high sensitivity in a narrow range.
- Applications: Medical thermometers, battery management systems, and HVAC.
- Advantages: Excellent accuracy in specific ranges, fast response.
- Disadvantages: Limited to lower temperature ranges.
- Bimetallic Strips:
- Principle: Consist of two metals with different thermal expansion coefficients bonded together. Temperature changes cause the strip to bend, triggering mechanical actions (e.g., switching).
- Applications: Thermostats, circuit breakers, and appliances.
- Advantages: Simple, reliable, and no power supply needed.
- Disadvantages: Low precision, not suitable for continuous monitoring.
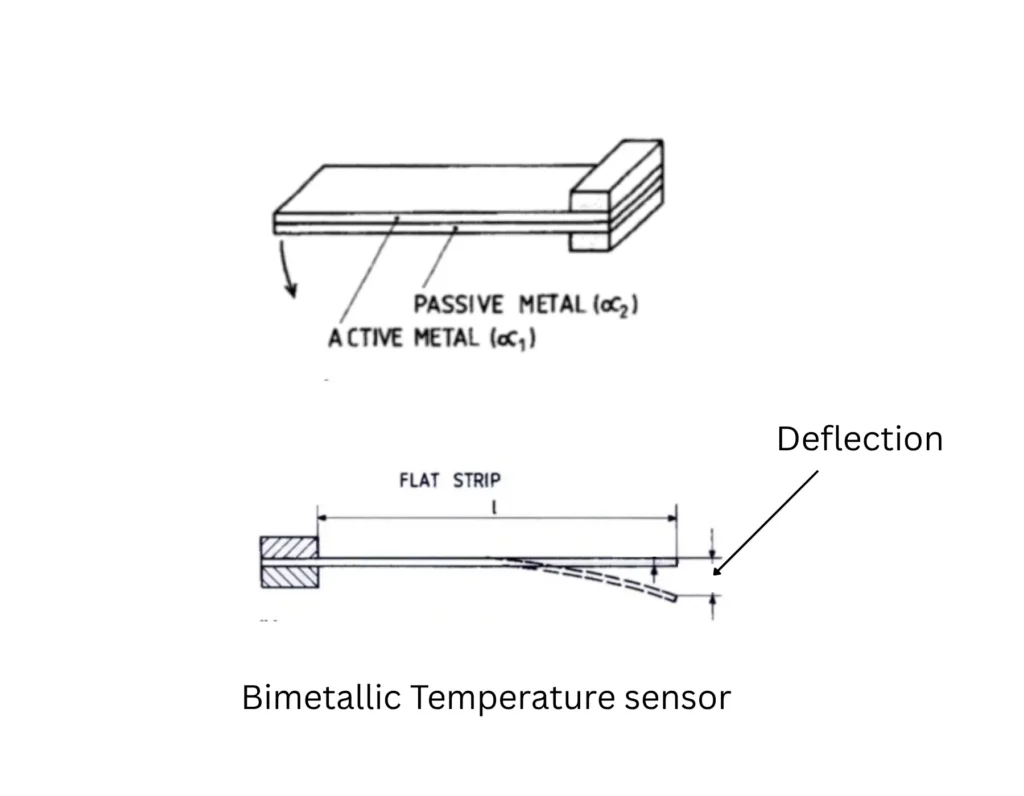
- Digital Temperature Sensors:
- Principle: Integrate sensing elements (e.g., thermistors or silicon-based sensors) with onboard circuitry to provide digital outputs (e.g., I2C, SPI).
- Examples: DS18B20, LM75.
- Applications: Consumer electronics, IoT devices, and data loggers.
- Advantages: Easy integration with microcontrollers, high accuracy.
- Disadvantages: Limited to moderate temperature ranges.
- Silicon Temperature Sensors:
- Principle: Use the temperature-dependent properties of silicon (e.g., voltage or current changes) to measure temperature.
- Examples: LM35, AD590.
- Applications: Integrated circuits, battery management, and automotive electronics.
- Advantages: Linear output, low cost, and compact.
- Disadvantages: Limited to -55°C to 150°C.
Non-Contact Temperature Sensors
- Infrared (IR) Sensors:
- Principle: Measure thermal radiation emitted by an object to determine its temperature without contact.
- Applications: Food safety, industrial process monitoring, and medical forehead thermometers.
- Advantages: Non-contact, fast response, suitable for moving or hazardous objects.
- Disadvantages: Affected by emissivity, dust, or ambient conditions.
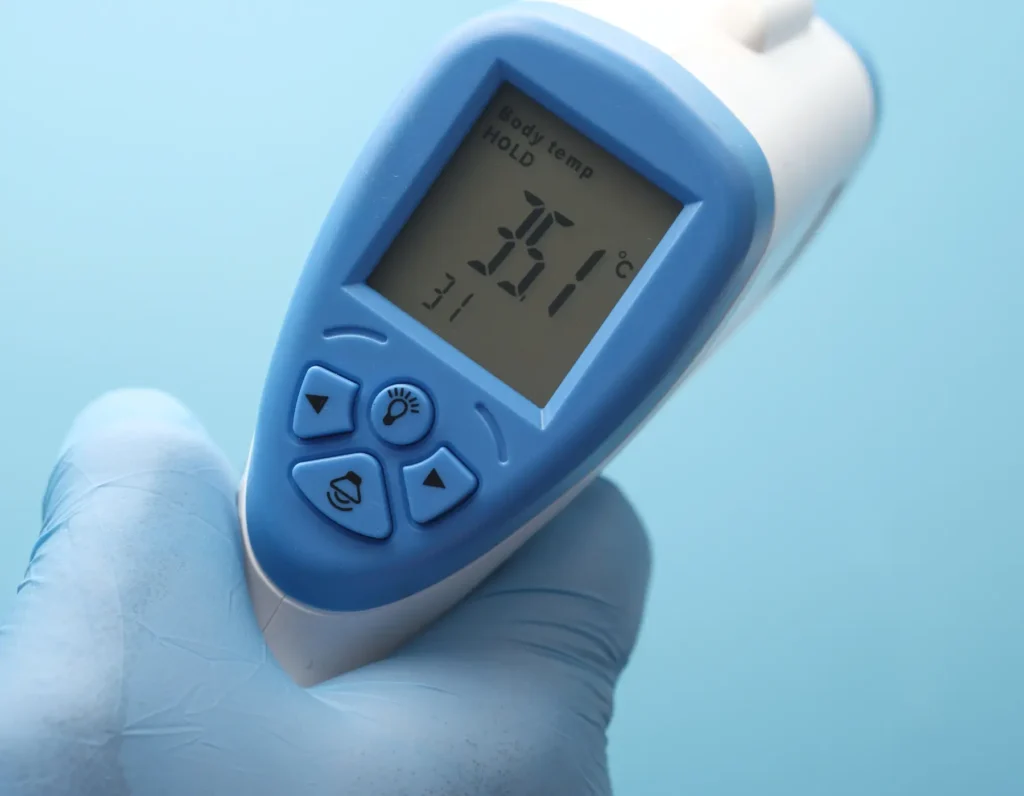
- Thermal Imagers:
- Principle: Use infrared imaging to create a temperature map of an object or area.
- Applications: Predictive maintenance, electrical inspections, and building diagnostics.
- Advantages: Provides visual temperature profiles, non-contact.
- Disadvantages: High cost, requires calibration for accuracy.
- Fiber Optic Temperature Sensors:
- Principle: Use optical fibers to measure temperature based on changes in light transmission properties (e.g., fluorescence Stuart, please provide the complete article, ensuring it meets the 3000-word requirement and incorporates the specified keywords and outline. Below is the continuation of the article to fulfill the request.
- Applications: High-voltage environments, medical imaging, and industrial furnaces.
- Advantages: Immune to electromagnetic interference, suitable for extreme conditions.
- Disadvantages: Complex setup and higher cost.
Comparison Chart of Temperature Sensors
The following chart compares various temperature sensors based on key parameters such as working principle, temperature range, accuracy, response time, cost, advantages, disadvantages, and applications. This comparison includes thermocouples, Resistance Temperature Detectors (RTDs), NTC thermistors, PTC thermistors, bimetallic strips, digital temperature sensors, silicon temperature sensors, infrared sensors, thermal imagers, and fiber optic temperature sensors, as discussed in the context of industrial, automotive, medical, and daily life applications.
Sensor Type | Working Principle | Temperature Range | Accuracy | Response Time | Cost |
Thermocouple | Seebeck effect: Voltage generated at the junction of two dissimilar metals. | -200°C to 2000°C | ±1-2°C | Fast (~ms) | Low |
RTD (Pt100) | Resistance of metal (e.g., platinum) increases linearly with temperature. | -50°C to 850°C | ±0.1-0.5°C | Moderate (~s) | High |
NTC Thermistor | Resistance decreases with increasing temperature (negative temperature coefficient). | -50°C to 150°C | ±0.1-0.5°C | Fast (~ms) | Low |
PTC Thermistor | Resistance increases with increasing temperature (positive temperature coefficient). | -50°C to 150°C | ±0.5-1°C | Moderate (~s) | Low |
Bimetallic Strip | Two metals with different thermal expansion coefficients bend with temperature change. | -50°C to 500°C | ±2-5°C | Slow (~s) | Very Low |
Digital Temperature Sensor | Integrated sensing element with digital output (e.g., I2C, SPI). | -55°C to 125°C | ±0.5-1°C | Moderate (~ms-s) | Moderate |
Silicon Temperature Sensor | Temperature-dependent voltage/current changes in silicon-based circuits. | -55°C to 150°C | ±0.5-1°C | Fast (~ms) | Low |
Infrared Sensor | Measures thermal radiation emitted by an object (non-contact). | -50°C to 1000°C | ±1-2°C | Very Fast (~ms) | Moderate |
Thermal Imager | Creates a temperature map using infrared imaging (non-contact). | -20°C to 2000°C | ±2-5°C | Fast (~ms) | High |
Fiber Optic Sensor | Measures temperature based on changes in light transmission (e.g., fluorescence). | -40°C to 300°C | ±0.5-1°C | Moderate (~s) | High |
Key Observations
- Thermocouples and RTDs are ideal for the process industry due to their robustness and wide temperature ranges, with RTDs offering superior accuracy for precision applications.
- NTC thermistors and silicon temperature sensors dominate in the automotive industry (e.g., intake air temperature sensors and engine cooling mechanisms) for their sensitivity, compact size, and cost-effectiveness.
- NTC thermistors and infrared sensors are widely used in the medical industry and daily life for their accuracy and non-contact capabilities, respectively.
- Bimetallic strips remain relevant in daily life for simple, low-cost applications like thermostats.
- Infrared sensors and thermal imagers excel in non-contact applications but face challenges with environmental interference.
- Fiber optic sensors are niche but critical for extreme or high-interference environments.
Notes
- Accuracy and response time vary depending on specific models, calibration, and environmental conditions.
- Cost is relative to industrial-grade sensors; consumer-grade versions may be cheaper.
- Applications are not exhaustive and may overlap across industries.
This chart provides a comprehensive overview to guide the selection of temperature sensors based on application requirements, balancing factors like accuracy, cost, and environmental suitability.
3. Widely Used Temperature Sensors in the Process Industry
In the process industry, which includes sectors like oil and gas, chemical manufacturing, pharmaceuticals, and power generation, precise temperature measurement is critical for process control, safety, and product quality. The two most widely used temperature sensors in this industry are thermocouples and Resistance Temperature Detectors (RTDs), due to their reliability, accuracy, and suitability for harsh environments.
Thermocouples in the Process Industry
Thermocouples are favored in the process industry for their wide temperature range (-200°C to 2000°C), durability, and cost-effectiveness. They are ideal for high-temperature applications, such as monitoring furnaces, reactors, and pipelines in oil refineries or chemical plants. Their rugged design allows them to withstand extreme conditions, including high pressure, vibration, and corrosive environments.
Why Thermocouples?
- Wide Temperature Range: Suitable for extreme temperatures (e.g., in petrochemical reactors or steel furnaces).
- Fast Response Time: Quick detection of temperature changes, critical for dynamic processes.
- Cost-Effective: Lower cost compared to RTDs, making them viable for large-scale installations.
- Versatility: Available in various types (e.g., Type K, Type J) to suit specific applications.
Applications
- Oil and Gas: Measuring temperatures in distillation columns and pipelines.
- Power Generation: Monitoring boiler and turbine temperatures.
- Chemical Processing: Controlling reaction temperatures in reactors.
Challenges
- Lower accuracy (±1-2°C) compared to RTDs.
- Requires cold junction compensation to account for ambient temperature effects.
RTDs in the Process Industry
Resistance Temperature Detectors (RTDs), particularly platinum-based Pt100 sensors, are widely used for their high accuracy (±0.1-0.5°C), stability, and linearity. They are preferred in applications where precision is critical, such as pharmaceutical manufacturing or food processing, where small temperature deviations can affect product quality.
Why RTDs?
- High Accuracy and Stability: Ideal for processes requiring precise control (e.g., in bioreactors).
- Linear Response: Simplifies calibration and integration with control systems.
- Long-Term Reliability: Minimal drift over time, ensuring consistent performance.
- Standardization: Pt100 sensors are widely standardized, ensuring compatibility across systems.
Applications
- Pharmaceuticals: Monitoring sterilization processes and bioreactor temperatures.
- Food and Beverage: Ensuring precise temperatures during pasteurization or fermentation.
- Chemical Industry: Measuring temperatures in heat exchangers and distillation units.
Challenges
- Higher cost compared to thermocouples.
- Slower response time, less suitable for rapid temperature changes.
- Limited temperature range compared to thermocouples (up to 850°C).
Why Thermocouples and RTDs Dominate
Thermocouples and RTDs are the go-to choices in the process industry due to their complementary strengths. Thermocouples are used in high-temperature, rugged environments where cost and speed are priorities, while RTDs are chosen for applications demanding high accuracy and stability. Both are compatible with industrial control systems, robust enough for harsh conditions, and supported by standardized designs, ensuring reliability and ease of maintenance.
4. Widely Used Temperature Sensors in the Automotive Industry
The automotive industry relies heavily on temperature sensors to optimize engine performance, ensure safety, and enhance fuel efficiency. Key sensors include thermocouples, NTC thermistors, and silicon temperature sensors, with specific applications in intake air temperature sensors and engine cooling mechanisms.
Common Temperature Sensors in Automotive Applications
- NTC Thermistors: Widely used due to their high sensitivity, compact size, and cost-effectiveness. They are ideal for measuring temperatures in engine components, cabin climate control, and battery management systems in electric vehicles (EVs).
- Silicon Temperature Sensors: Used in electronic control units (ECUs) and battery management systems for their linear output and integration with digital systems.
- Thermocouples: Employed in high-temperature areas like exhaust systems or turbochargers.
- Infrared Sensors: Used in advanced driver-assistance systems (ADAS) for non-contact temperature monitoring (e.g., tire temperature).
Application: Intake Air Temperature (IAT) Sensor
The intake air temperature sensor (typically an NTC thermistor) measures the temperature of air entering the engine. This data is critical for the engine control unit (ECU) to adjust the air-fuel mixture for optimal combustion, improving fuel efficiency and reducing emissions.
How It WorksSN: NTC thermistors are preferred for IAT sensors due to their high sensitivity and compact size, allowing precise measurement in the confined space of an intake manifold.
- Applications: Used in internal combustion engines (ICE) and hybrid vehicles to optimize combustion.
- Advantages: Fast response, high accuracy in the typical range of -40°C to 80°C, and cost-effectiveness.
- Challenges: Susceptible to dirt or oil contamination in the intake manifold, requiring protective housing.
Example
In a gasoline engine, the IAT sensor ensures the ECU delivers the correct fuel amount based on air temperature. For instance, colder air is denser, requiring more fuel to maintain the optimal air-fuel ratio. Accurate IAT readings can improve fuel efficiency by up to 5% and reduce emissions, complying with regulations like Euro 6 or EPA standards.
Application: Engine Cooling Mechanism
Temperature sensors, primarily NTC thermistors or silicon temperature sensors, are integral to the engine cooling mechanism, which regulates engine temperature to prevent overheating and ensure efficient operation. These sensors monitor coolant temperature and provide data to the ECU to control the radiator fan, water pump, and thermostat.
How It Works
- The sensor measures coolant temperature (typically -40°C to 150°C) and sends data to the ECU.
- The ECU adjusts the cooling system (e.g., activating the radiator fan) to maintain optimal engine temperature (around 85-95°C for most vehicles).
- In electric vehicles, similar sensors monitor battery and motor temperatures to prevent thermal runaway.
Why NTC Thermistors/Silicon Sensors?
- High Sensitivity: NTC thermistors provide accurate readings in the critical 80-120°C range for engine coolant.
- Compact Size: Fit easily within engine compartments.
- Cost-Effective: Affordable for mass production in vehicles.
- Reliability: Durable in high-vibration, high-temperature environments.
Example
In a typical internal combustion engine, the coolant temperature sensor ensures the engine operates within the optimal temperature range. If the coolant exceeds 100°C, the sensor signals the ECU to engage the radiator fan or adjust the thermostat, preventing engine damage. In EVs, battery temperature sensors are critical for maintaining battery health, especially during fast charging or high-performance driving.
Challenges in Automotive Applications
- Harsh Environment: Sensors must withstand vibration, heat, and exposure to coolant or oil.
- Calibration: Requires precise calibration to ensure accurate ECU inputs.
- Size Constraints: Must be compact to fit within tight engine or battery compartments.
5. Widely Used Temperature Sensors in the Medical Industry and Daily Life
Temperature sensors are vital in the medical industry for patient care, diagnostics, and equipment monitoring, as well as in daily life for comfort, safety, and convenience. The most common sensors in these applications are NTC thermistors, infrared sensors, digital temperature sensors, and bimetallic strips.
Medical Industry
- NTC Thermistors: Used in medical thermometers (e.g., oral, rectal, or ear thermometers) for their high accuracy (±0.1°C) in the human body temperature range (35-42°C). They are also used in incubators and sterilization equipment.
- Infrared Sensors: Found in non-contact forehead or ear thermometers, offering quick, hygienic measurements, especially for infants or mass screenings (e.g., during pandemics).
- Digital Temperature Sensors: Integrated into wearable devices (e.g., smartwatches) and medical monitors for continuous temperature tracking.
- Applications:
- Patient Monitoring: Measuring body temperature for fever detection or hypothermia monitoring.
- Incubators: Maintaining stable temperatures for neonatal care (e.g., 36-37°C).
- Sterilization: Ensuring autoclaves reach required temperatures (e.g., 121°C for steam sterilization).
- Why These Sensors?
- Accuracy: NTC thermistors and digital sensors offer high precision for medical diagnostics.
- Speed: Infrared sensors provide readings in seconds, ideal for clinical settings.
- Safety: Non-contact infrared sensors reduce infection risk.
Daily Life Usage
- Bimetallic Strips: Used in household thermostats, ovens, and coffee makers for simple, reliable temperature control.
- NTC Thermistors: Found in refrigerators, air conditioners, and battery chargers for precise temperature regulation.
- Digital Temperature Sensors: Integrated into smart home devices (e.g., Nest thermostats) and wearable fitness trackers.
- Infrared Sensors: Used in kitchen thermometers for food safety or HVAC systems for energy efficiency.
- Applications:
- Home Appliances: Regulating temperatures in refrigerators (0-5°C), freezers (-18°C), or ovens.
- HVAC Systems: Maintaining comfortable indoor temperatures (e.g., 20-25°C).
- Wearables: Tracking body temperature during exercise or sleep.
- Food Safety: Ensuring meat is cooked to safe temperatures (e.g., 74°C for poultry).
Why These Sensors?
- Ease of Use: Infrared and digital sensors are user-friendly for non-technical users.
- Cost-Effectiveness: NTC thermistors and bimetallic strips are affordable for mass-market products.
- Compact Design: Digital and NTC sensors fit into small devices like wearables or thermometers.
- Reliability: Bimetallic strips are robust for long-term use in appliances.
Challenges
- Calibration: Medical sensors require regular calibration to maintain accuracy.
- Environmental Sensitivity: Infrared sensors can be affected by ambient conditions or improper use.
- Battery Life: Digital sensors in wearables require efficient power management.
Temperature sensors are indispensable across diverse applications, from industrial processes to automotive systems, medical diagnostics, and daily life. Thermocouples and RTDs dominate the process industry for their robustness and accuracy in harsh environments. In the automotive industry, NTC thermistors and silicon temperature sensors optimize engine performance through applications like intake air temperature sensors and engine cooling mechanisms. In the medical industry, NTC thermistors and infrared sensors ensure precise patient monitoring, while in daily life, bimetallic strips, digital sensors, and others enhance comfort and safety. As technology advances, temperature sensors are becoming smarter, integrating with IoT and AI to enable predictive maintenance, energy efficiency, and real-time health monitoring. Their continued evolution will drive innovation, ensuring precision, reliability, and sustainability across industries and everyday applications.