In the realm of industrial automation, sensors form the backbone of data acquisition and process control, enabling systems to monitor, analyze, and respond to environmental conditions with precision. From manufacturing plants to environmental monitoring systems, sensors are indispensable for ensuring efficiency, safety, and reliability. This article provides an in-depth exploration of various types of sensors, focusing on their principles, applications, and significance in industrial settings. The discussion covers pressure sensors, temperature sensors, level sensors, chemical analyzers (including pH analyzers, conductivity analyzers, gas chromatographs, oxygen analyzers, dew point analyzers, TOC analyzers, and NOX/SOX analyzers), eddy current sensors, motion sensors, proximity sensors, and optical sensors.
1. What is a Sensor?
A sensor is a device that detects and measures physical, chemical, or environmental properties and converts them into readable signals, typically electrical or digital outputs. These signals are used by control systems, such as programmable logic controllers (PLCs) or distributed control systems (DCS), to make informed decisions, trigger actions, or monitor processes. Sensors act as the interface between the physical world and automated systems, enabling real-time data collection for applications ranging from industrial automation to environmental monitoring.
Sensors operate on the principle of transduction, where a physical or chemical stimulus (e.g., pressure, temperature, or light) is converted into an electrical signal, such as voltage, current, or digital data. They are designed to be highly sensitive, accurate, and reliable, often functioning in harsh industrial environments. The versatility of sensors makes them critical in industries like manufacturing, oil and gas, pharmaceuticals, and environmental management.
2. Types of Sensors
The diversity of industrial applications has led to the development of numerous sensor types, each tailored to measure specific parameters. Broadly, sensors can be categorized based on the properties they measure, such as physical (e.g., pressure, temperature), chemical (e.g., pH, gas concentration), or electromagnetic (e.g., light, magnetic fields). Some sensors are active, requiring an external power source, while others are passive, generating signals without external power. Below, we explore key sensor types relevant to industrial automation.
3. Pressure Sensor
A pressure sensor measures the force exerted by a gas or liquid on a surface, typically expressed in units like pascal (Pa), bar, or psi. These sensors are essential in industries where pressure monitoring is critical, such as oil and gas, aerospace, and manufacturing.
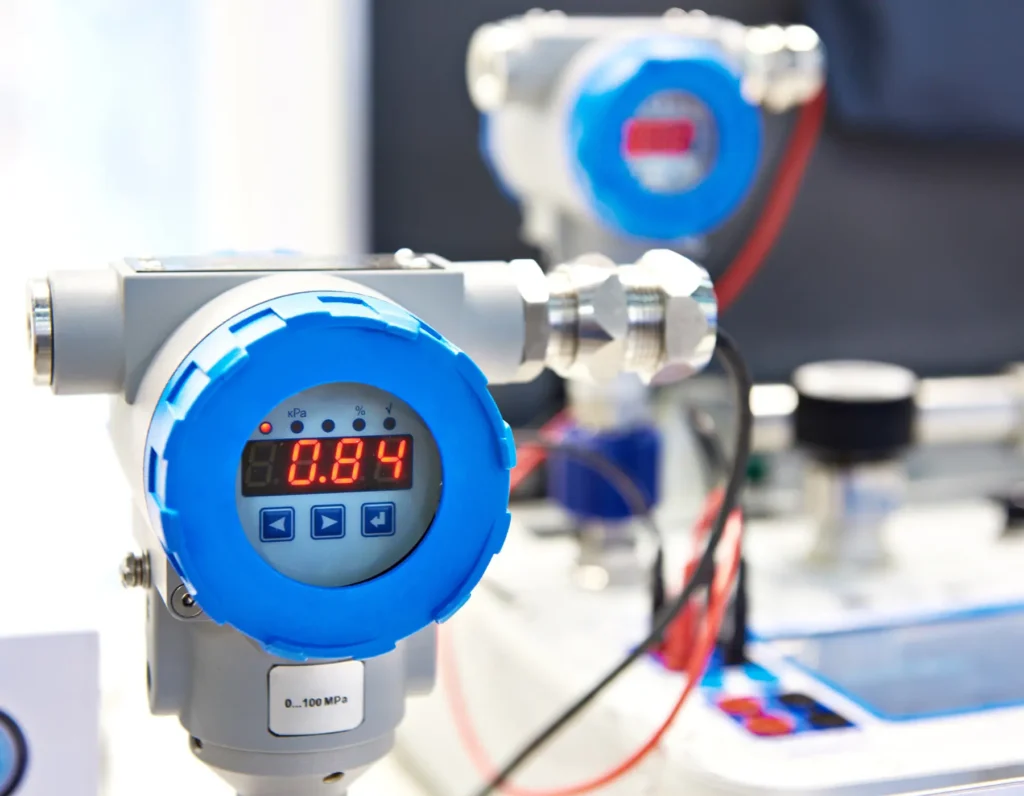
Working Principle
Pressure sensors typically operate using piezoresistive, capacitive, or piezoelectric principles. Piezoresistive sensors, for example, use a diaphragm that deforms under pressure, altering the resistance of embedded strain gauges. This change is converted into an electrical signal proportional to the pressure. Capacitive sensors measure changes in capacitance caused by diaphragm movement, while piezoelectric sensors generate voltage in response to pressure-induced mechanical stress.
Applications
- Oil and Gas: Monitoring pipeline pressure to prevent leaks or bursts.
- HVAC Systems: Ensuring optimal air pressure in ventilation systems.
- Automotive: Measuring tire pressure or engine manifold pressure.
- Medical Devices: Monitoring blood pressure or respiratory systems.
Advantages
- High accuracy and sensitivity.
- Wide range of pressure measurement (from vacuum to high-pressure systems).
- Robust design for harsh environments.
Challenges
- Calibration drift over time.
- Sensitivity to temperature variations, requiring compensation.
A temperature sensor measures the thermal energy of a system, providing data in units like Celsius, Fahrenheit, or Kelvin. These sensors are ubiquitous in industries requiring precise thermal management, such as food processing, pharmaceuticals, and electronics manufacturing.
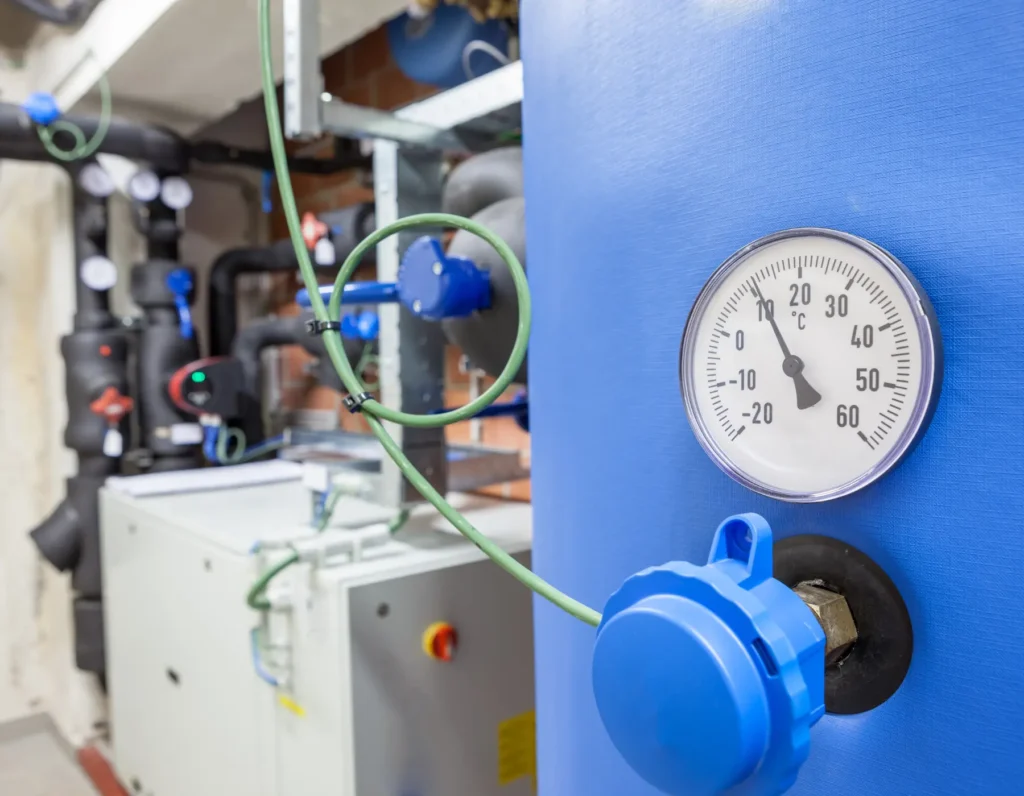
Types and Working Principles
- Thermocouples: Generate a voltage based on the temperature difference between two metal junctions (Seebeck effect).
- Resistance Temperature Detectors (RTDs): Measure resistance changes in materials (e.g., platinum) as temperature varies.
- Thermistors: Use temperature-dependent resistance changes in ceramic or polymer materials.
- Infrared Sensors: Detect thermal radiation emitted by objects for non-contact measurement.
Applications
- Manufacturing: Monitoring furnace or reactor temperatures.
- HVAC: Regulating building climate control.
- Food Industry: Ensuring safe storage conditions.
- Electronics: Preventing overheating in circuits.
Advantages
- Wide temperature range (e.g., -200°C to 2000°C for thermocouples).
- High accuracy (especially RTDs).
- Non-contact options (infrared sensors) for hazardous environments.
Challenges
- Limited accuracy in extreme conditions for some types.
- Calibration requirements for long-term reliability.
5. Level Sensor
A level sensor measures the level of liquids, solids, or slurries in containers, tanks, or silos. These sensors are critical in industries like water treatment, oil refining, and chemical processing to ensure proper inventory management and process control.
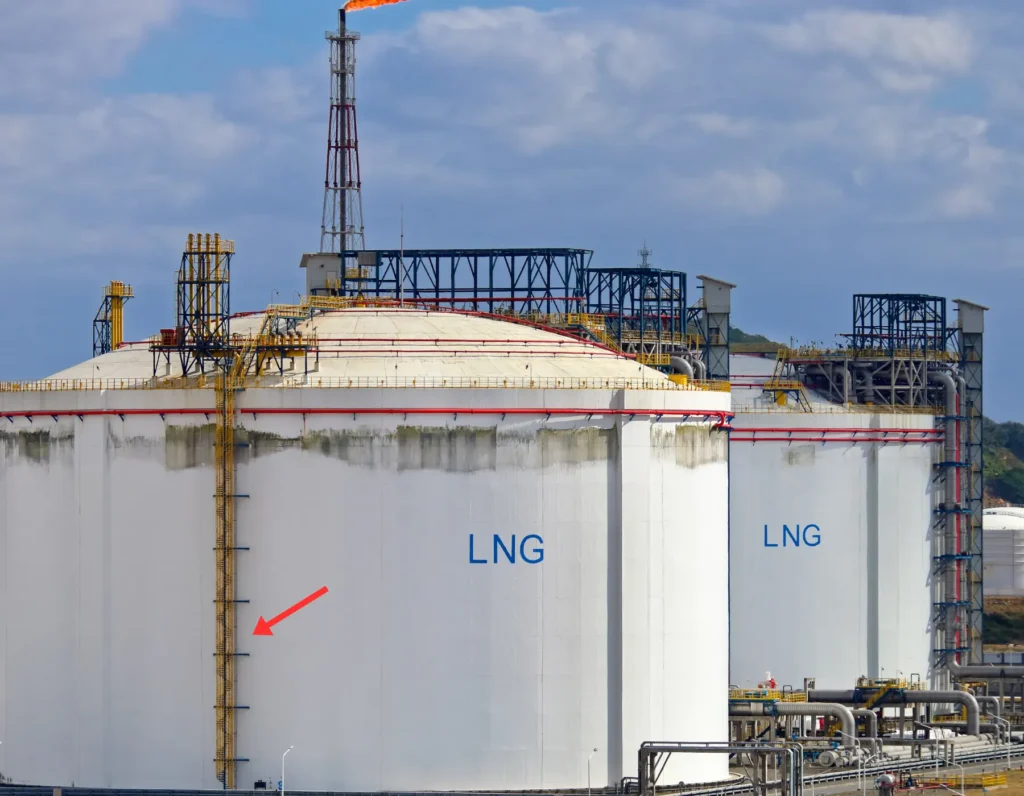
Types and Working Principles
- Ultrasonic Level Sensors: Use sound waves to measure the distance to the surface of the material.
- Capacitive Level Sensors: Detect changes in capacitance caused by the presence of material.
- Float Sensors: Use a buoyant device that rises or falls with the liquid level.
- Radar Level Sensors: Employ microwave signals for non-contact level measurement.
Applications
- Water Treatment: Monitoring tank levels in wastewater facilities.
- Oil and Gas: Measuring crude oil levels in storage tanks.
- Food and Beverage: Ensuring consistent ingredient levels in mixing tanks.
- Pharmaceuticals: Controlling liquid levels in bioreactors.
Advantages
- Versatility across liquids, solids, and slurries.
- Non-contact options for corrosive or high-temperature materials.
- High reliability in continuous monitoring.
Challenges
- Interference from foam, vapor, or turbulence in ultrasonic sensors.
- Calibration for different material properties.
6. Chemical Analyzers
Chemical analyzers are specialized sensors designed to measure the chemical composition or properties of gases, liquids, or solids. These devices are vital in industries like environmental monitoring, chemical manufacturing, and wastewater treatment. Below, we explore key types of chemical analyzers.
(i) pH Analyzer
A pH analyzer measures the acidity or alkalinity of a solution, expressed on a scale from 0 to 14. It typically consists of a pH electrode (glass or ion-selective) and a reference electrode, which generate a voltage proportional to the hydrogen ion concentration.
Applications
- Water Treatment: Ensuring optimal pH for drinking water or wastewater.
- Pharmaceuticals: Controlling pH in drug formulation.
- Food Industry: Monitoring pH in fermentation processes.
Advantages
- High sensitivity to small pH changes.
- Real-time monitoring for process control.
Challenges
- Electrode fouling in dirty or viscous solutions.
- Regular calibration and maintenance.
(ii) Conductivity Analyzer
A conductivity analyzer measures the ability of a solution to conduct electricity, which correlates with its ion concentration. It uses electrodes to apply an electric field and measure the resulting current.
Applications
- Water Quality: Detecting salinity or contamination in water.
- Chemical Processing: Monitoring ionic content in solutions.
- Boiler Systems: Preventing scale buildup by monitoring water conductivity.
Advantages
- Robust for harsh environments.
- Wide range of conductivity measurements.
Challenges
- Sensitivity to temperature variations.
- Electrode contamination in high-solid environments.
(iii) Gas Chromatographs
Gas chromatographs separate and analyze gas mixtures to identify and quantify their components. They use a stationary phase and a carrier gas to separate compounds based on their interaction with the stationary phase.
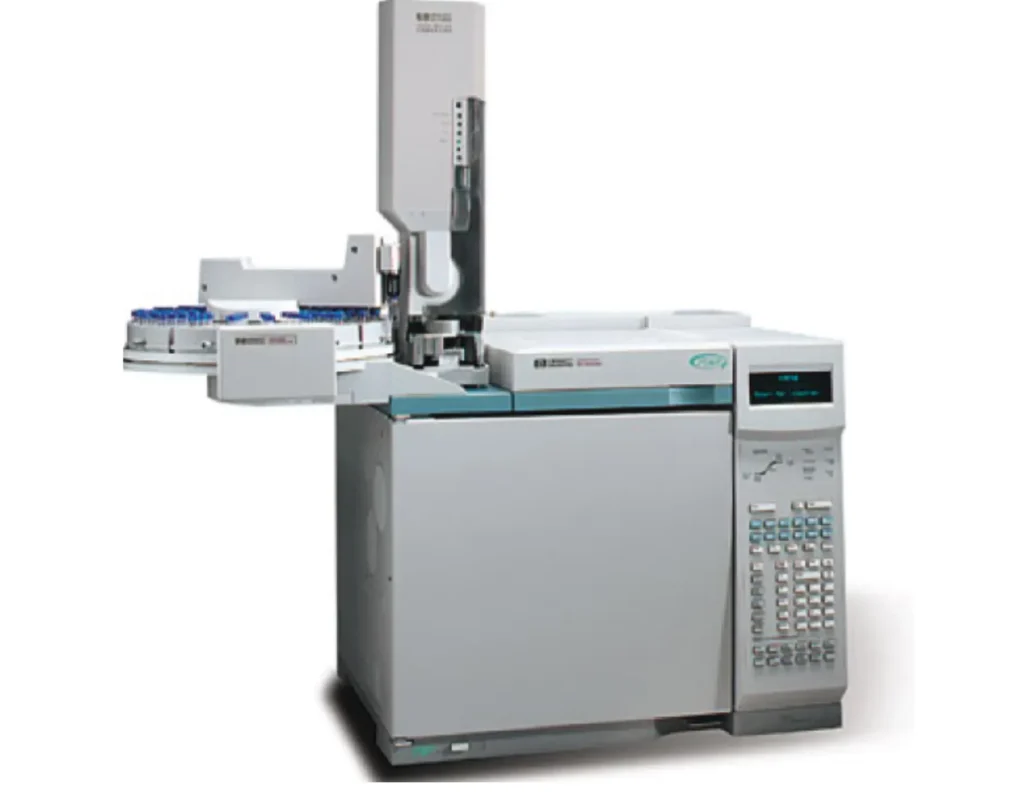
Applications
- Oil and Gas: Analyzing hydrocarbon compositions.
- Environmental Monitoring: Detecting volatile organic compounds (VOCs).
- Pharmaceuticals: Ensuring purity of gaseous intermediates.
Advantages
- High precision in identifying complex mixtures.
- Suitable for trace-level detection.
Challenges
- Complex setup and maintenance.
- Requires skilled operators.
(iv) Oxygen Analyzer
An oxygen analyzer measures the concentration of oxygen in gases or liquids, often using electrochemical, paramagnetic, or zirconia-based sensors.
Applications
- Combustion Control: Optimizing fuel efficiency in boilers.
- Medical: Monitoring oxygen levels in respiratory systems.
- Environmental: Measuring dissolved oxygen in water bodies.
Advantages
- High accuracy in low-oxygen environments.
- Fast response times.
Challenges
- Sensor degradation over time.
- Interference from other gases.
(v) Dew Point Analyzer
A dew point analyzer measures the temperature at which air becomes saturated, causing water vapor to condense. It is critical for controlling moisture in industrial processes.
Applications
- Compressed Air Systems: Preventing corrosion in pipelines.
- Pharmaceuticals: Ensuring dry conditions for sensitive materials.
- HVAC: Controlling humidity in buildings.
Advantages
- Precise moisture control.
- Wide range of dew point measurements.
Challenges
- Sensitivity to contaminants like oil or dust.
- Calibration complexity.
(vi) TOC Analyzer
A TOC analyzer (Total Organic Carbon analyzer) measures the amount of organic carbon in water, indicating contamination levels. It uses oxidation techniques (e.g., UV or combustion) to convert organic carbon to carbon dioxide for measurement.
Applications
- Water Treatment: Monitoring organic pollutants in wastewater.
- Pharmaceuticals: Ensuring water purity for drug manufacturing.
- Semiconductors: Controlling water quality in production processes.
Advantages
- High sensitivity to low organic levels.
- Real-time monitoring capabilities.
Challenges
- High cost of equipment.
- Maintenance of oxidation systems.
(vii) NOX/SOX Analyzer
NOX/SOX analyzers measure nitrogen oxides (NOX) and sulfur oxides (SOX) in exhaust gases, critical for environmental compliance. They use techniques like chemiluminescence (for NOX) or fluorescence (for SOX).
Applications
- Power Plants: Monitoring emissions for regulatory compliance.
- Automotive: Testing exhaust gases in vehicles.
- Industrial Furnaces: Controlling combustion emissions.
Advantages
- High accuracy for trace gas detection.
- Compliance with environmental regulations.
Challenges
- Complex calibration requirements.
- Sensitivity to gas stream conditions.
7. Eddy Current Sensor
An eddy current sensor measures the distance or properties of conductive materials using electromagnetic induction. When an alternating current passes through a coil, it generates a magnetic field that induces eddy currents in nearby conductive objects, altering the coil’s impedance.
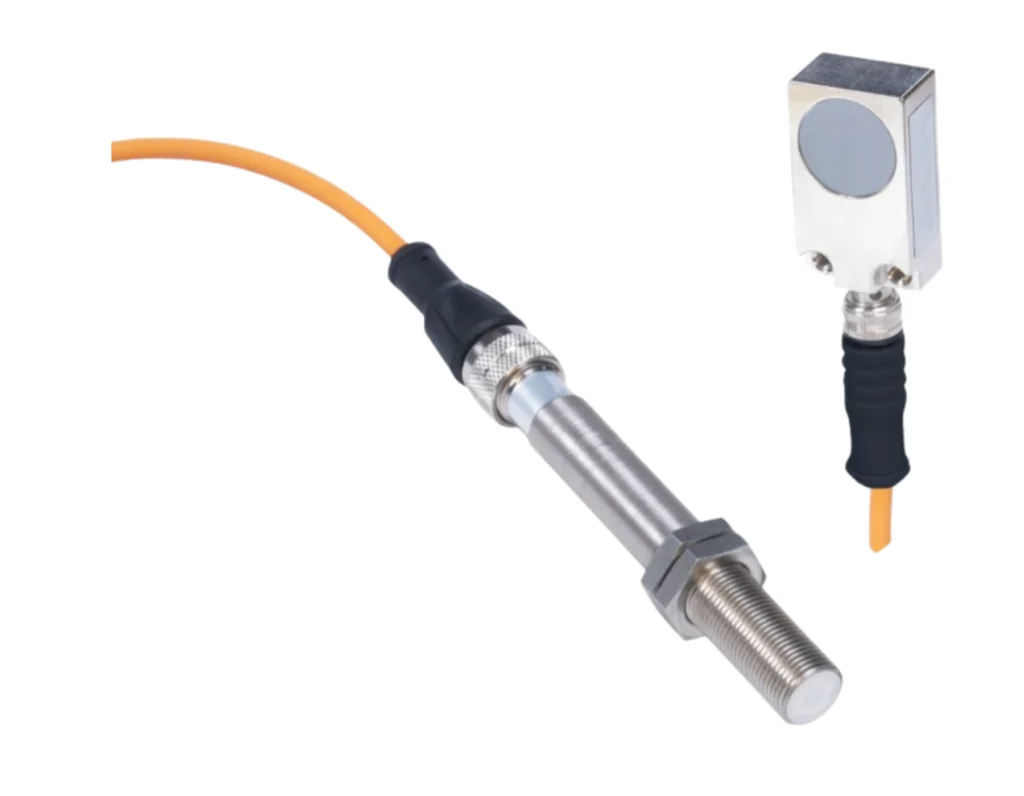
Applications
- Manufacturing: Detecting cracks or defects in metal parts.
- Aerospace: Measuring turbine blade clearance.
- Automotive: Monitoring shaft position or vibration.
Advantages
- Non-contact measurement.
- High sensitivity to small changes in distance or material properties.
Challenges
- Limited to conductive materials.
- Sensitivity to environmental magnetic fields.
8. Motion Sensors
Motion sensors detect movement or changes in position, often using technologies like infrared, ultrasonic, or microwave signals. They are widely used for automation, security, and energy management.
Types and Applications
- Passive Infrared (PIR): Detects heat emitted by moving objects (e.g., in security systems).
- Ultrasonic: Uses sound waves to detect motion (e.g., in automatic doors).
- Microwave: Emits microwave signals to detect movement (e.g., in traffic monitoring).
Advantages
- Wide range of detection methods.
- Suitable for both indoor and outdoor applications.
Challenges
- False triggers from environmental factors (e.g., heat sources for PIR).
- Limited range for some technologies.
9. Proximity Sensors
Proximity sensors detect the presence of objects without physical contact, using technologies like capacitive, inductive, or ultrasonic principles.
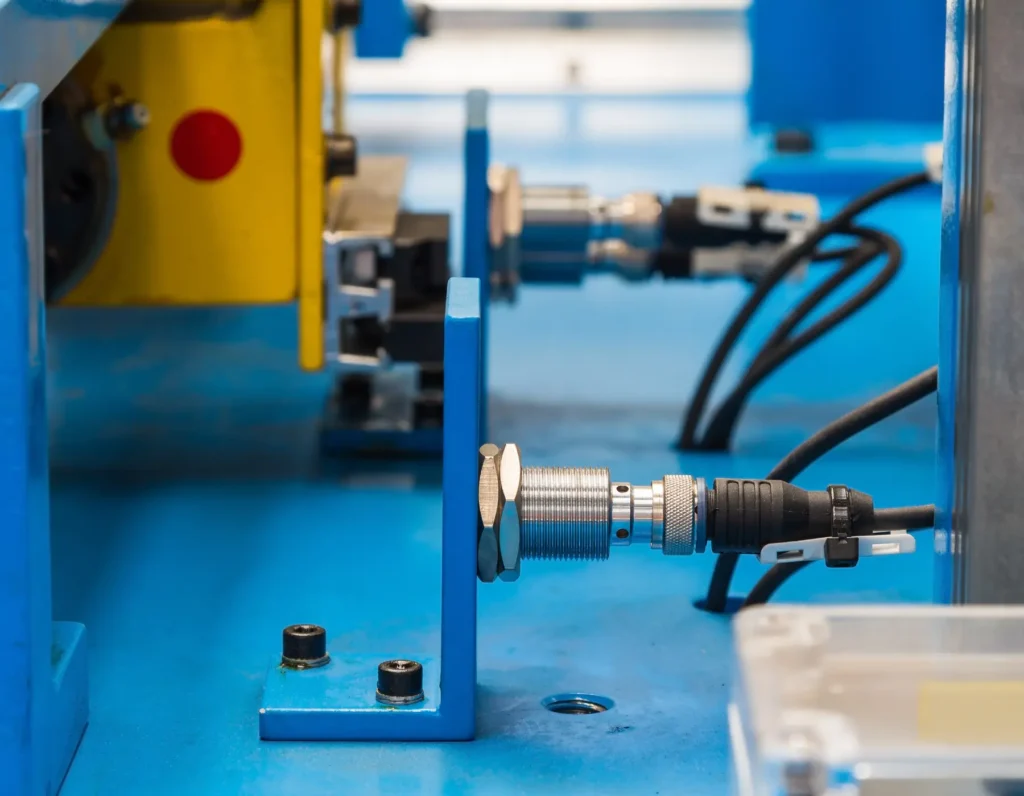
Applications
- Manufacturing: Detecting objects on conveyor belts.
- Automotive: Parking assistance systems.
- Robotics: Obstacle detection.
Advantages
- Non-contact operation.
- High durability in harsh environments.
Challenges
- Limited detection range.
- Sensitivity to material properties (e.g., inductive sensors work only with metals).
10. Optical Sensors
Optical sensors use light to measure properties like distance, position, or intensity. They operate using principles such as reflection, absorption, or interference of light.
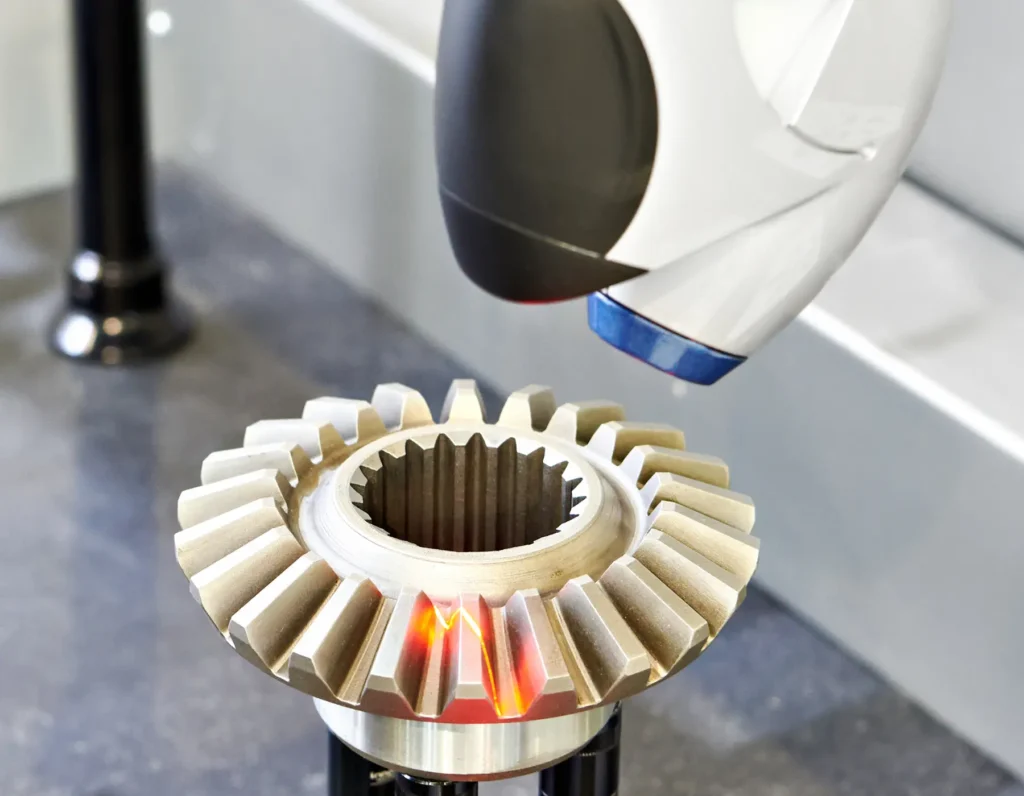
Types and Applications
- Photodetectors: Measure light intensity (e.g., in solar panels).
- Fiber Optic Sensors: Detect changes in light transmission (e.g., in structural monitoring).
- Laser Sensors: Measure distance or position with high precision (e.g., in robotics).
Advantages
- High precision and speed.
- Non-contact measurement for delicate applications.
Challenges
- Sensitivity to dust, smoke, or ambient light.
- Higher cost for advanced systems.
Sensors are the cornerstone of modern industrial automation, enabling precise monitoring and control of diverse processes. From pressure sensors ensuring safe pipeline operations to temperature sensors maintaining optimal conditions, and chemical analyzers like pH analyzers, conductivity analyzers, gas chromatographs, oxygen analyzers, dew point analyzers, TOC analyzers, and NOX/SOX analyzers ensuring environmental and process compliance, each sensor type plays a critical role. Additionally, eddy current sensors, motion sensors, proximity sensors, and optical sensors enhance automation by providing non-contact, high-precision measurements. As industries embrace technologies like IoT and AI, sensors will continue to evolve, driving efficiency, sustainability, and innovation across sectors.